How To Solder Automotive Wires Together
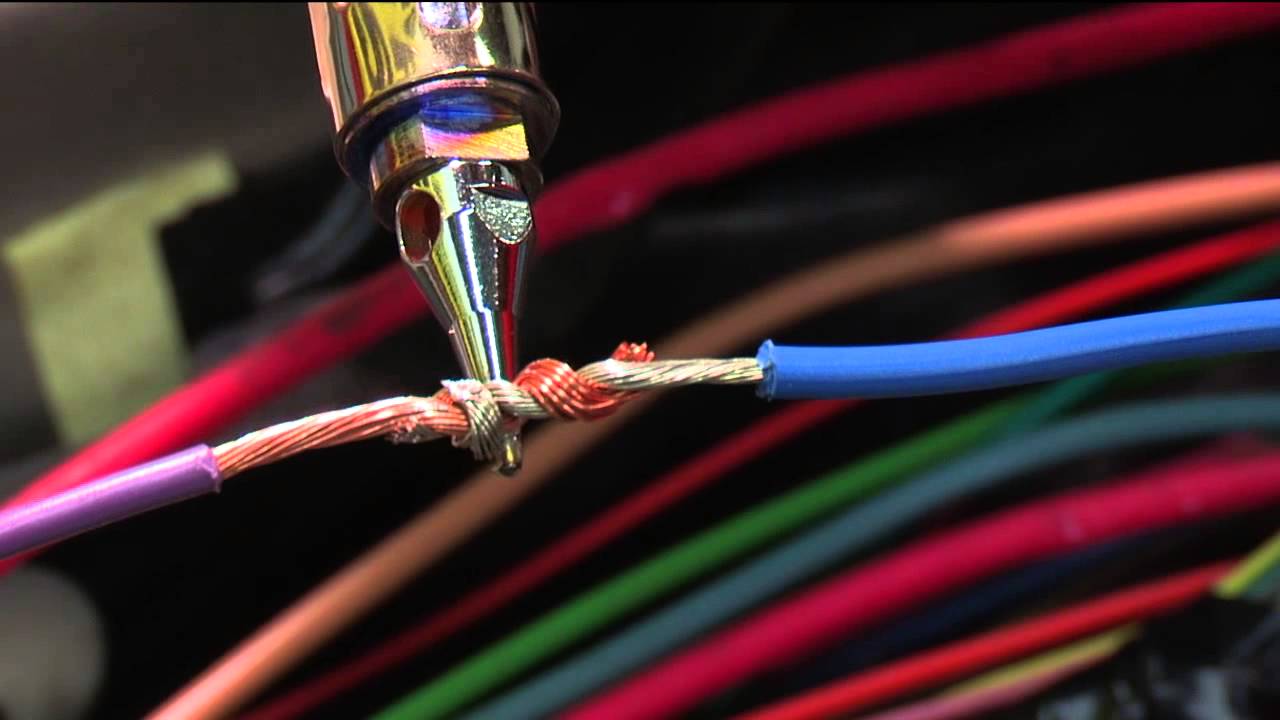
Automotive-grade stranded wire thats the same gage as the old wire.
How to solder automotive wires together. This solder melts at about 370 F. Then use a pair of pliers to push the metal tap down into both wires flush with the body of the connector and snap the cover over the tap. Begingroup Cut and solder allows heat-shrink sleeving over join.
Tin the end of both wires by clamping them in your third hand jig and holding the iron under the wire and allowing solder to flow into the wire. First you need to strip the wires then add your heat shrink tubing physically connect the wiressolder the wires together and then shrink that heat shrink tubing to make a waterproof connection. Tap the end of the 6337 solder on top of the wire splice so the solder melts down into the wires.
Make sure your soldering iron is fully heated and touch the tip to the end of one of the wires. Tin the tip of the iron and then clean it with a sponge before heating the wire. Work from multiple angles and make sure to get thorough coverage.
Automotive wiring should be soldered and protected properly in order to withstand all types of weather rain snow and salt. If the wire is stranded twist the strands together with your fingers. The first step is you need to strip your wires.
Be sure to place the shrink-wrap tubing on prior to connecting the wires if that is. The process for soldering 3 wires together is the same as splicing 2 4 or even 10 of them. Next get ready with your solder and.
Slide the existing wire into the open side of the connector then put the end of the wire you wish to connect to it into the other side. Heat up the joint and melt the solder with the wire not the soldering iron. Automotive applications use 6040 containing 60 tin and 40 lead.